Why outboard engine manufacturers use roller bearings vs. friction bearings?
- Mike Hill
- Jul 11, 2024
- 2 min read
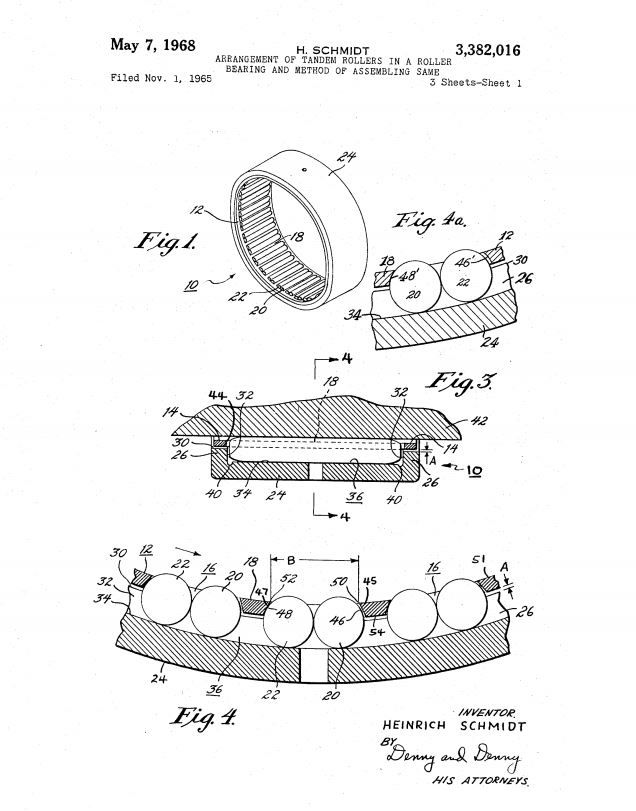
Outboard engine manufacturers often use roller bearings instead of friction bearings (such as plain bearings or bushings) in 2-stroke engines for several reasons:
Load Handling Capability: Roller bearings, particularly needle roller bearings, can handle higher radial and axial loads compared to friction bearings. This is important in outboard engines where the crankshaft experiences varying and sometimes significant loads due to the nature of marine propulsion.
Durability and Reliability: Roller bearings are generally more durable and have a longer service life than friction bearings. They are designed to withstand higher stresses and provide consistent performance over extended periods, which is crucial for the reliability of outboard engines operating in harsh marine environments.
Reduced Friction and Heat Generation: Roller bearings typically exhibit lower friction compared to friction bearings, which reduces energy loss and heat generation. In a 2-stroke outboard engine, minimizing friction helps optimize fuel efficiency and overall performance.
Compact Design: Roller bearings can often be designed to have a more compact profile compared to friction bearings of similar load capacity. This compactness is beneficial for packaging within the constrained spaces of outboard engines.
Maintenance Considerations: Roller bearings generally require less maintenance compared to friction bearings. They are less susceptible to wear and typically do not require lubrication or replacement as frequently, reducing downtime and maintenance costs for outboard engine operators.
Industry Standard: Roller bearings have become a standard choice in modern outboard engine designs due to their proven performance and reliability. They are well-suited to handle the operational demands and stresses encountered in marine applications.
Overall, the use of roller bearings in 2-stroke outboard engines is driven by their superior load handling capabilities, durability, reduced friction, and suitability for marine environments. These factors collectively contribute to improved performance, efficiency, and reliability of outboard engines.
*Picture here is the original patent for the Upper Main Bearing found in the Mercury 2.4 Liter 2-Stroke V6 Outboards with 1 3/8" top journal on the crank.
AKA the OEM part number 93496, 31-93496T or RBC TJ-75117-11 filed under Patent 3382016 "Arrangement of tandem rollers in a roller bearing and method of assembling same".
This bearing was designed to handle 8,500 RPMs and was selected for the motor based on:
Load Distribution: Tandem roller bearings are designed to handle heavy radial and axial loads simultaneously. They distribute the load across a larger surface area compared to single-row bearings, which can improve bearing life and performance.
High Load Capacity: They are capable of supporting higher radial and axial loads, making them suitable for applications where significant forces are acting in multiple directions.
Reliability: These bearings have been used for many years in various industrial applications, indicating their reliability and established performance in demanding conditions.
留言